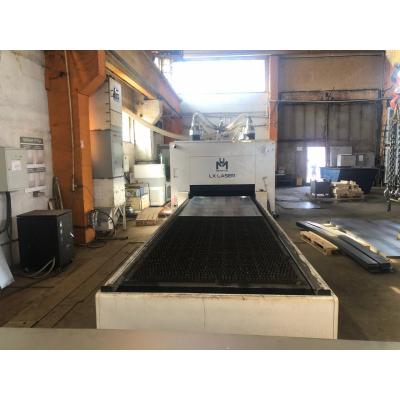
Лазерная резка металла
Современные методики раскроя металлических полотен включают применение лазерных технологий. Механическое воздействие на металл в масштабах конвейерного производства уже в прошлом: стандартное распиливание оставляет неровности на швах и в точности значительно уступает лазеру. Последний всемирно известен как LBC – Laser Beam Cutting. Эта технология включает все виды лазерной резки, осуществляемой на высокоточном оборудовании с ЧПУ. Метод позволяет создавать детали сложных форм максимально точно, соответственно заданным габаритам. Применение шаблонов обеспечивает динамический раскрой листового металла и непрерывные бизнес-процессы.
Методики лазерной резки
Все методики лазерной резки металла основаны на точечном направлении интенсивного лазера по строго заданному контуру. Он запрограммирован в оборудовании с ЧПУ. Процесс резки лазером включает стабильное охлаждение разрезаемого проема газом, что предотвращает чрезмерное расплавление краев и деформацию заготовки.
Суть технологии проста: целенаправленный лазерный луч разрушает металлическую поверхность в точках соприкосновения, тем самым «разрезая» полотно так, как настроена программа ЧПУ. На контурах прохождения луча остается условный, практически незаметный, максимально ровный шов. Его ширина соответствует диаметру лазерного вектора. По факту рассечения получаются очень тонкие, точные, аккуратные.
Такая методика положительно зарекомендовала себя в промышленном производстве по всему миру и практически вытеснила использование стандартных пил. Резка металла лазером классифицируется на несколько видов.
Разделение или плавление
Самый распространенный способ. Он подходит практически для всех металлов и требует профессионального подхода в использовании оборудования. Необходимо корректно задать температуру и длительность воздействия соответственно виду разрезаемого полотна. По ходу движения луча расплавленный металл выдувается одним из применяемых в этих случаях газом (зачастую азотом) подобно стандартной газорезке (в которой продувание происходит кислородом). Благодаря активной струе газа, образуемые кромки рассекаемой поверхности моментально охлаждаются, предотвращается лишнее плавление. Луч перемещается по строго заданному алгоритму и способен создавать разнообразные контуры.
Термораскалывание или горение
Обеспечивает высокую температуру на поверхности металла и горение. Из-за большого термического напряжения этот способ подходит для раскроя исключительно черных металлов, например, чугуна. Заготовки цветных металлов и некоторых видов стали имеют в составе легирующие примеси, поэтому разрезать их термораскалыванием не рекомендуется – вследствие прохождения луча края металла становятся немного обгоревшими.
Скрайбирование или испарение
Этот метод применяется редко. В основном, в отношении листового металла небольшой толщины, полупроводников или керамики. Объясняется это спецификой технологии. В отличие от динамического лазерного луча двух ранее рассмотренных способов LBC, здесь режим резки имеет импульсный характер.
Преимущества лазерной резки металла
Технология LBC имеет множество положительных аспектов, среди них:
- Улучшенная точность распилов по контуру по сравнению с механической резкой – нет необходимости в дополнительной обработке кромок.
- Диапазон толщины листового металла варьирует от 1 до 4 см.
- Выбор раскроя металла по способу исполнения – 2D или 3D (трехмерный), в зависимости от требуемого результата.
- Возможность применения станков с ЧПУ и соответственно – полноценной автоматизации производства с параллельной сложностью контуров.
- Производительность раскроя способна достигать скорости до 25 м в минуту.
В отличие от механического распила, в этой технологии меньше требований к фиксации распиливаемых полотен и нюансов в выполнении процесса. Например, не приходится периодически смачивать места распила. Благодаря тонким швам, расход полотен рационализируется, уменьшая издержки производства.
Виды оборудования
Каждый лазерный станок отличается характеристиками. Но все они одинаковы по наличию основных составляющих. Станки содержат излучатель, управляющий модуль с соответствующей системой, узловой агрегат (он в нужных направлениях передвигает лазер над заготовками).
Мощность лазера нарушает целостность металла в месте контакта, предполагает последующую продувку этого сегмента специальным газом. Благодаря высокой температуре поверхность заготовки плавится или испаряется в конкретных точках соприкосновения лазера. Структура металла способна разрушаться до сквозных отверстий. Лазерное оборудование классифицируется на несколько видов:
- Газовые модели предполагают использование углекислого газа либо его смеси с гелием или азотом.
- Твердотельные конструкции включают рубиновый или другой подобный стержень, как основной способ передачи световой энергии, трансформирующейся в лазер.
- Газодинамические системы основаны на применении оксида углерода как основного активного вещества для резки, разогреваемого в температурном режиме от 720˚C до 2730˚C. Такие агрегаты имеют специальную конструкцию для ускорения газового потока и охлаждения с основной целью – предотвратить перегрев металла.
Параметры, эффективность станка напрямую влияет на конечный результат – качество изготавливаемых металлических изделий. Полноценная функциональность оборудования и правильная настройка параметров в каждом случае обеспечивает продукции точные и правильные контуры – согласно заданным габаритам. Чтобы минимизировать вероятность брака, стоит учитывать этот фактор.
Если оборудование неправильно настроено или допущены весомые погрешности раскроя, на кромках распилов формируется так называемый облой. Этот дефект связан с неправильными термическими настройками программного обеспечения и перегревом разрезаемой заготовки. По краям остаются капли, неровности или следы чрезмерно расплавленного металла.
В результате формирования облоя страдает качество изделий. Для устранения дефекта используют механическую обработку, потенциально нарушающую заданные габариты, геометрию металлических изделий. Поэтому специалисты считают облой серьезным нарушением технологии производства, способным привести к браку всей партии листового металла. Чтобы производственный процесс был непрерывным, нужно не только правильно отрегулировать параметры работы оборудования, но и выполнять следующие действия:
- Своевременно охлаждать места разрезов газовым потоком.
- Обеспечить альтернативный вариант на случай отключения основного источника электропитания.
- Проводить систематическую юстировку оптики.
Перед началом работы целесообразно убедиться в достаточной мощности лазера – она должна обеспечивать рассечение заготовок соответствующей толщины и разновидности металла.
Порядок выполнения лазерной резки
Использование углекислого газа в технологии LBC способствует предотвращению окисления металла: инертная среда позволяет поступать кислороду из окружающей атмосферы. Характеристики каждого реза улучшаются за счет продува газом. Этапы выполнения лазерной резки:
- разработка эскиза (шаблона) будущей модели;
- перенос форм и нюансов макета в подходящий электронный вид;
- создание пробной модели в тестовом режиме;
- анализ тестового изделия на предмет соответствия заданным контурам и габаритам;
- отладка параметров (при необходимости);
- активация автоматизированного производства.
Создание и отладка шаблонов имеет свои нюансы. Готовый проект для загрузки в программное обеспечение станка должен соответствовать нужному масштабу, подходить по формату. Программа резки настраивается таким образом, чтобы рассечение не происходило по одним и тем же контурам дважды.
К единственному минусу технологии стоит отнести ее стоимость, из-за которой изготавливать единичные изделия нецелесообразно. Поэтому лазерная резка металла экономически оправдана при массовом автоматизированном производстве с минимизацией издержек и себестоимости выпускаемой продукции.
Область применения и стоимость резки
Лазерная резка позволяет осуществлять раскрой не только металлов, но и любых материалов – за исключением полотен с зеркальными поверхностями, отражающими лучи. Станок способен разрезать стекло и оргстекло, ДВП, ДСП, древесные, полимерные, пластиковые и комбинированные полотна. Технология востребована в следующих сферах:
- в автомобиле-, судостроении;
- в легкой, обувной промышленности;
- в производстве электронных и электротехнических устройств;
- в создании объектов декора, дизайна;
- в изготовлении рекламной, сувенирной или различной бытовой продукции.
Стоимость резки лазером рассчитывается с помощью квалифицированных программ. Цена зависит от вида металла (цветные изделия сложнее обрабатывать), его толщины, сложности макета.